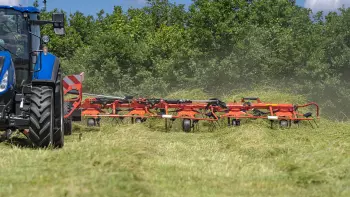
The soil is not scraped and the forage quality is preserved
The GF 13003 T tedder follows ground unevenness like its narrow-width counterparts.
This excellent ground following is made possible by the exclusive GSC (Ground Save Control) system. This system is characterized by a new concept allowing to have a very small distance between the wheels of the frame and the rotors. For the user, it is the assurance of having excellent ground following responsiveness, even on the most uneven terrain.
Some exceptional features:
This excellent ground following is made possible by the exclusive GSC (Ground Save Control) system. This system is characterized by a new concept allowing to have a very small distance between the wheels of the frame and the rotors. For the user, it is the assurance of having excellent ground following responsiveness, even on the most uneven terrain.
Some exceptional features:
- When working, the weight of the frame rests on the wide transport wheels.
- The small-diameter rotors ensure efficient turning and quick drying of the forage.
- No need to invest in and adjust an additional guide wheel